Budowa maszyn pneumatycznych to temat, który zyskuje na znaczeniu w przemyśle i technologii. Maszyny te wykorzystują energię sprężonego powietrza do wykonywania różnorodnych zadań, co czyni je niezwykle efektywnymi i wszechstronnymi. W procesie budowy takich maszyn kluczowe jest zrozumienie zasad działania układów pneumatycznych, które obejmują kompresory, zawory, siłowniki oraz różnego rodzaju akcesoria. Kompresor jest sercem systemu, odpowiedzialnym za sprężanie powietrza i dostarczanie go do pozostałych elementów układu. Zawory kontrolują przepływ powietrza, a siłowniki przekształcają energię pneumatyczną w ruch mechaniczny. Właściwe zaprojektowanie i wykonanie tych komponentów ma kluczowe znaczenie dla efektywności całego systemu. W kontekście budowy maszyn pneumatycznych istotne są także materiały, z których są one wykonane, ponieważ muszą one wytrzymać wysokie ciśnienia oraz różne warunki pracy.
Jakie są główne komponenty maszyn pneumatycznych?
Maszyny pneumatyczne składają się z wielu kluczowych komponentów, które współpracują ze sobą w celu osiągnięcia zamierzonych efektów. Do najważniejszych elementów należy kompresor, który spręża powietrze i dostarcza je do systemu. Istnieją różne typy kompresorów, takie jak tłokowe czy śrubowe, które różnią się sposobem działania oraz zastosowaniem. Kolejnym istotnym elementem są zawory, które regulują przepływ sprężonego powietrza w układzie. Zawory te mogą być ręczne lub automatyczne, a ich wybór zależy od specyfiki aplikacji. Siłowniki pneumatyczne to kolejny kluczowy komponent, który przekształca energię pneumatyczną w ruch mechaniczny. Mogą mieć różne kształty i rozmiary, a ich dobór jest uzależniony od wymagań konkretnej aplikacji. Dodatkowo w budowie maszyn pneumatycznych często wykorzystuje się filtry powietrza oraz osuszacze, które zapewniają czystość i odpowiednią jakość sprężonego powietrza.
Jakie są zalety stosowania maszyn pneumatycznych w przemyśle?
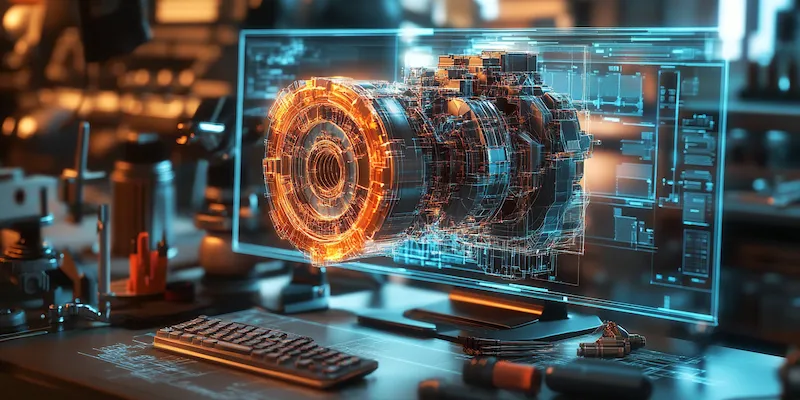
Stosowanie maszyn pneumatycznych w przemyśle niesie ze sobą wiele korzyści, które przyczyniają się do zwiększenia efektywności produkcji oraz obniżenia kosztów operacyjnych. Jedną z głównych zalet jest ich prostota obsługi oraz łatwość w integracji z istniejącymi systemami produkcyjnymi. Maszyny te charakteryzują się również dużą niezawodnością oraz niskimi kosztami utrzymania, co czyni je atrakcyjnym rozwiązaniem dla wielu przedsiębiorstw. Ponadto maszyny pneumatyczne są znane z wysokiej prędkości działania oraz precyzyjnego sterowania ruchem, co pozwala na realizację skomplikowanych procesów produkcyjnych. Warto również zwrócić uwagę na ich wszechstronność – mogą być wykorzystywane w różnych branżach, od przemysłu motoryzacyjnego po spożywczy. Dzięki możliwości łatwego dostosowania parametrów pracy do specyficznych potrzeb produkcji, maszyny pneumatyczne stają się coraz bardziej popularnym wyborem w nowoczesnych zakładach przemysłowych.
Jakie zastosowania mają maszyny pneumatyczne w różnych branżach?
Maszyny pneumatyczne znajdują szerokie zastosowanie w różnych branżach przemysłowych dzięki swojej wszechstronności oraz efektywności działania. W przemyśle motoryzacyjnym są wykorzystywane do montażu elementów samochodowych oraz do testowania ich wytrzymałości. W branży spożywczej maszyny te służą do pakowania produktów oraz transportu surowców w procesach produkcyjnych. W sektorze budowlanym maszyny pneumatyczne znajdują zastosowanie w narzędziach takich jak młoty udarowe czy wiertarki pneumatyczne, co znacznie zwiększa wydajność prac budowlanych. Również w przemyśle elektronicznym maszyny te odgrywają istotną rolę przy montażu delikatnych komponentów elektronicznych, gdzie precyzja i szybkość działania są kluczowe. Dodatkowo w logistyce i magazynowaniu maszyny pneumatyczne ułatwiają transport towarów oraz automatyzację procesów załadunku i rozładunku.
Jakie są najnowsze trendy w budowie maszyn pneumatycznych?
Najnowsze trendy w budowie maszyn pneumatycznych koncentrują się na innowacyjnych rozwiązaniach technologicznych oraz zwiększonej efektywności energetycznej tych urządzeń. W ostatnich latach obserwuje się rosnące zainteresowanie automatyzacją procesów produkcyjnych przy użyciu systemów pneumatycznych, co pozwala na zwiększenie wydajności oraz redukcję kosztów pracy. Wprowadzenie inteligentnych systemów sterowania umożliwia precyzyjne zarządzanie pracą maszyn oraz monitorowanie ich stanu w czasie rzeczywistym. Kolejnym trendem jest rozwój materiałów o wysokiej wytrzymałości i niskiej wadze, co przekłada się na mniejsze zużycie energii oraz dłuższą żywotność komponentów. Ponadto coraz większą uwagę przykłada się do kwestii ekologicznych – projektanci starają się tworzyć maszyny o mniejszym wpływie na środowisko poprzez optymalizację procesów sprężania powietrza oraz minimalizację strat energii. Warto również zauważyć rosnącą popularność rozwiązań mobilnych i kompaktowych, które umożliwiają łatwe przemieszczanie maszyn oraz ich adaptację do różnych warunków pracy.
Jakie są wyzwania związane z budową maszyn pneumatycznych?
Budowa maszyn pneumatycznych wiąże się z różnymi wyzwaniami, które inżynierowie i projektanci muszą uwzględnić na każdym etapie procesu. Jednym z głównych problemów jest zapewnienie odpowiedniej szczelności układów pneumatycznych, ponieważ nawet niewielkie nieszczelności mogą prowadzić do znacznych strat energii oraz obniżenia efektywności działania maszyny. Właściwe dobranie materiałów oraz technologii montażu jest kluczowe dla utrzymania wysokiej wydajności systemu. Kolejnym wyzwaniem jest konieczność dostosowania maszyn do różnorodnych warunków pracy, takich jak zmienne temperatury, wilgotność czy obecność zanieczyszczeń w powietrzu. Inżynierowie muszą także brać pod uwagę bezpieczeństwo użytkowników, projektując maszyny w sposób minimalizujący ryzyko wypadków oraz awarii. Dodatkowo, w miarę postępu technologicznego, rośnie potrzeba integracji maszyn pneumatycznych z nowoczesnymi systemami automatyki i robotyki, co wymaga ciągłego doskonalenia umiejętności i wiedzy specjalistów w tej dziedzinie.
Jakie są koszty budowy maszyn pneumatycznych?
Koszty budowy maszyn pneumatycznych mogą się znacznie różnić w zależności od wielu czynników, takich jak skomplikowanie projektu, zastosowane materiały oraz technologie produkcji. Na początku procesu należy uwzględnić wydatki związane z zakupem komponentów, takich jak kompresory, zawory czy siłowniki. Koszt tych elementów może być znaczny, zwłaszcza jeśli wymagane są specjalistyczne rozwiązania dostosowane do konkretnych potrzeb przemysłowych. Dodatkowo należy wziąć pod uwagę koszty pracy związane z projektowaniem i montażem maszyn. W przypadku bardziej zaawansowanych systemów pneumatycznych konieczne może być zatrudnienie wysoko wykwalifikowanych specjalistów, co również wpływa na ogólny koszt budowy. Warto również pamiętać o kosztach eksploatacji maszyn, które obejmują zużycie energii, konserwację oraz ewentualne naprawy.
Jakie są kluczowe aspekty projektowania maszyn pneumatycznych?
Projektowanie maszyn pneumatycznych to proces skomplikowany i wieloaspektowy, który wymaga uwzględnienia wielu czynników wpływających na ich funkcjonalność i efektywność. Kluczowym aspektem jest analiza wymagań aplikacji, która pozwala na określenie parametrów technicznych maszyny oraz jej komponentów. W tym etapie istotne jest zrozumienie specyfiki procesu produkcyjnego oraz oczekiwań użytkowników. Kolejnym ważnym elementem jest dobór odpowiednich materiałów, które muszą charakteryzować się wysoką wytrzymałością na ciśnienie oraz odpornością na korozję. Projektanci muszą także zadbać o ergonomię urządzenia, aby zapewnić komfort pracy operatorom oraz minimalizować ryzyko wystąpienia urazów. Dodatkowo nie można zapominać o aspektach związanych z bezpieczeństwem – maszyny powinny być wyposażone w odpowiednie zabezpieczenia oraz systemy monitorujące ich stan techniczny.
Jakie są przyszłościowe kierunki rozwoju technologii pneumatycznej?
Przyszłość technologii pneumatycznej zapowiada się niezwykle obiecująco dzięki ciągłemu rozwojowi innowacyjnych rozwiązań oraz rosnącemu zainteresowaniu automatyzacją procesów przemysłowych. Jednym z kluczowych kierunków rozwoju jest integracja systemów pneumatycznych z nowoczesnymi technologiami cyfrowymi i Internetem Rzeczy (IoT). Dzięki temu możliwe będzie monitorowanie stanu maszyn w czasie rzeczywistym oraz optymalizacja ich pracy na podstawie analizy danych. Kolejnym trendem jest rozwój inteligentnych siłowników pneumatycznych, które będą mogły dostosowywać swoje parametry pracy do zmieniających się warunków otoczenia oraz potrzeb aplikacji. Ponadto coraz większą uwagę przykłada się do kwestii ekologicznych – inżynierowie pracują nad rozwiązaniami mającymi na celu minimalizację zużycia energii oraz redukcję emisji hałasu generowanego przez maszyny pneumatyczne. Również rozwój materiałów kompozytowych o wysokiej wytrzymałości i niskiej wadze będzie miał istotny wpływ na konstrukcję urządzeń pneumatycznych.
Jakie są najlepsze praktyki w zakresie konserwacji maszyn pneumatycznych?
Konserwacja maszyn pneumatycznych jest kluczowym elementem zapewniającym ich długotrwałą eksploatację oraz niezawodność działania. Istotne jest regularne przeprowadzanie przeglądów technicznych, które pozwalają na wykrycie potencjalnych usterek zanim staną się one poważnym problemem. W ramach konserwacji należy zwrócić szczególną uwagę na kontrolę szczelności układów pneumatycznych – nieszczelności mogą prowadzić do strat energii oraz obniżenia efektywności działania maszyny. Ważne jest także regularne czyszczenie filtrów powietrza oraz osuszaczy, aby zapewnić odpowiednią jakość sprężonego powietrza dostarczanego do systemu. Dodatkowo warto prowadzić dokumentację wszystkich przeprowadzonych prac konserwacyjnych oraz wymiany komponentów, co ułatwi zarządzanie serwisem urządzeń i pozwoli na szybsze reagowanie na ewentualne problemy. Należy również pamiętać o szkoleniu personelu obsługującego maszyny – dobrze przeszkoleni pracownicy są w stanie szybko zauważyć nieprawidłowości w działaniu urządzeń i podjąć odpowiednie kroki w celu ich naprawy lub zgłoszenia awarii.
Jakie są różnice między maszynami pneumatycznymi a hydraulicznymi?
Maszyny pneumatyczne i hydrauliczne to dwa różne typy urządzeń wykorzystywanych w przemyśle do wykonywania podobnych zadań mechanicznych, jednak różnią się one zasadniczo pod względem działania i zastosowania. Maszyny pneumatyczne wykorzystują sprężone powietrze jako medium robocze, co sprawia, że są lżejsze i łatwiejsze w obsłudze niż maszyny hydrauliczne, które opierają swoje działanie na cieczy hydraulicznej pod wysokim ciśnieniem. Dzięki temu maszyny pneumatyczne charakteryzują się mniejszymi wymaganiami przestrzennymi oraz prostszą konstrukcją. Z drugiej strony maszyny hydrauliczne oferują większą siłę roboczą i precyzyjniejsze sterowanie ruchem, co czyni je idealnym rozwiązaniem dla ciężkich aplikacji przemysłowych wymagających dużych obciążeń. Ponadto maszyny hydrauliczne są bardziej odporne na zmiany temperatury i wilgotności otoczenia niż ich pneumatyczne odpowiedniki.