Destylator przemysłowy to urządzenie, które odgrywa kluczową rolę w wielu procesach produkcyjnych, szczególnie w przemyśle chemicznym, petrochemicznym oraz spożywczym. Jego głównym zadaniem jest oddzielanie składników cieczy na podstawie różnicy ich temperatur wrzenia. Proces ten polega na podgrzewaniu mieszaniny, co powoduje parowanie substancji o niższej temperaturze wrzenia, a następnie skraplaniu pary w celu uzyskania czystego produktu. W przypadku destylacji frakcyjnej, która jest często stosowana w przemyśle, wykorzystuje się kolumny destylacyjne, które pozwalają na wielokrotne skraplanie i parowanie, co zwiększa efektywność separacji. Destylatory przemysłowe są projektowane z uwzględnieniem specyficznych potrzeb danej branży, co oznacza, że mogą mieć różne rozmiary i konfiguracje. W zależności od zastosowania, mogą być wykorzystywane do produkcji alkoholu, oczyszczania wody czy też odzyskiwania rozpuszczalników.
Jakie są rodzaje destylatorów przemysłowych i ich zastosowania
W przemyśle istnieje wiele różnych rodzajów destylatorów przemysłowych, które są dostosowane do specyficznych potrzeb produkcyjnych. Najpopularniejsze z nich to destylatory prostokątne, kolumnowe oraz próżniowe. Destylatory prostokątne są najczęściej stosowane w mniejszych zakładach produkcyjnych i charakteryzują się prostą budową oraz łatwością obsługi. Z kolei destylatory kolumnowe są bardziej skomplikowane i wykorzystywane w dużych instalacjach przemysłowych, gdzie konieczne jest uzyskanie wysokiej czystości produktów. Działają one na zasadzie wielokrotnego parowania i skraplania, co pozwala na efektywną separację składników. Destylatory próżniowe natomiast działają w obniżonym ciśnieniu, co umożliwia destylację substancji o wysokiej temperaturze wrzenia bez ich degradacji. Każdy z tych typów ma swoje unikalne zastosowania – od produkcji alkoholu po oczyszczanie chemikaliów czy recykling rozpuszczalników.
Jakie są kluczowe elementy konstrukcyjne destylatora przemysłowego
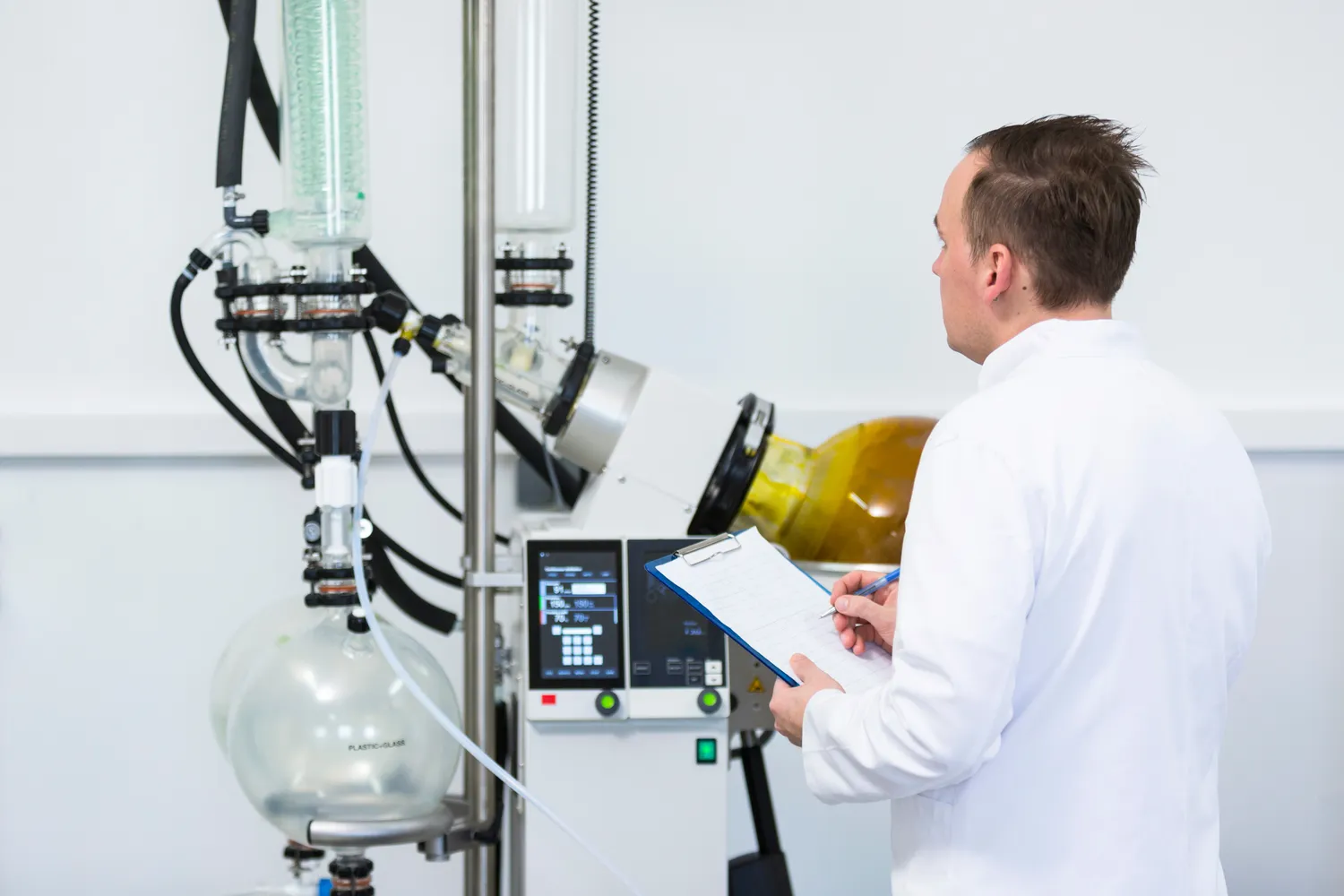
Konstrukcja destylatora przemysłowego składa się z kilku kluczowych elementów, które współpracują ze sobą w celu efektywnego przeprowadzenia procesu destylacji. Najważniejszym z nich jest zbiornik do podgrzewania cieczy, który może być wyposażony w różne źródła ciepła, takie jak elektryczność czy para wodna. Kolejnym istotnym elementem jest kolumna destylacyjna, która jest miejscem separacji składników na podstawie różnicy temperatur wrzenia. Wewnątrz kolumny znajdują się różnego rodzaju elementy wspomagające proces separacji, takie jak packingi czy tray’e, które zwiększają powierzchnię kontaktu między parą a cieczą. Po skropleniu pary produkt trafia do zbiornika odbiorczego, gdzie może być magazynowany lub kierowany do dalszej obróbki. Dodatkowo, nowoczesne destylatory często wyposażone są w systemy automatyzacji i monitoringu, które pozwalają na bieżące śledzenie parametrów pracy urządzenia oraz zapewniają optymalizację procesu.
Jakie są korzyści z używania nowoczesnych destylatorów przemysłowych
Nowoczesne destylatory przemysłowe oferują szereg korzyści, które przyczyniają się do poprawy efektywności procesów produkcyjnych oraz jakości finalnych produktów. Przede wszystkim dzięki zastosowaniu zaawansowanych technologii możliwe jest osiągnięcie wyższej wydajności separacji składników, co przekłada się na mniejsze straty surowców oraz niższe koszty operacyjne. Nowoczesne urządzenia często wyposażone są w systemy automatyzacji i monitoringu, co pozwala na bieżące dostosowywanie parametrów pracy do zmieniających się warunków produkcji. Dzięki temu można uniknąć problemów związanych z nieefektywnym działaniem urządzeń oraz zminimalizować ryzyko awarii. Ponadto nowoczesne destylatory charakteryzują się lepszą jakością uzyskiwanych produktów – dzięki precyzyjnej kontroli temperatury i ciśnienia możliwe jest uzyskanie substancji o wysokiej czystości chemicznej.
Jakie są najczęstsze problemy związane z destylatorami przemysłowymi
Destylatory przemysłowe, mimo swojej zaawansowanej technologii, mogą napotykać różne problemy, które wpływają na ich wydajność i jakość uzyskiwanych produktów. Jednym z najczęstszych problemów jest osadzanie się zanieczyszczeń w kolumnach destylacyjnych, co prowadzi do zmniejszenia efektywności separacji. Osady te mogą pochodzić z surowców używanych w procesie lub być wynikiem reakcji chemicznych zachodzących podczas destylacji. Regularne czyszczenie i konserwacja urządzeń są kluczowe dla utrzymania ich w dobrym stanie. Innym istotnym problemem jest niewłaściwe ustawienie parametrów pracy, takich jak temperatura czy ciśnienie, co może prowadzić do nieefektywnej separacji składników oraz obniżenia jakości produktów. Właściwe monitorowanie i automatyzacja procesów są niezbędne, aby uniknąć takich sytuacji. Dodatkowo, awarie elementów konstrukcyjnych, takich jak wymienniki ciepła czy pompy, mogą prowadzić do przestojów w produkcji oraz zwiększenia kosztów operacyjnych.
Jakie są wymagania dotyczące bezpieczeństwa w eksploatacji destylatorów przemysłowych
Bezpieczeństwo w eksploatacji destylatorów przemysłowych jest kluczowym aspektem, który należy uwzględnić na każdym etapie procesu produkcyjnego. Przede wszystkim, ze względu na wysokie temperatury oraz ciśnienia stosowane w tych urządzeniach, konieczne jest przestrzeganie rygorystycznych norm i standardów bezpieczeństwa. Właściwe zabezpieczenia mechaniczne, takie jak zawory bezpieczeństwa czy systemy awaryjnego wyłączania, powinny być integralną częścią konstrukcji destylatora. Ponadto, personel obsługujący urządzenia musi być odpowiednio przeszkolony w zakresie procedur bezpieczeństwa oraz reagowania na sytuacje awaryjne. Regularne audyty bezpieczeństwa oraz inspekcje techniczne są niezbędne do identyfikacji potencjalnych zagrożeń i ich eliminacji. Ważnym aspektem jest również odpowiednie zarządzanie substancjami chemicznymi wykorzystywanymi w procesie destylacji – należy zapewnić ich bezpieczne przechowywanie oraz transport.
Jakie innowacje technologiczne wpływają na rozwój destylatorów przemysłowych
W ostatnich latach obserwuje się dynamiczny rozwój technologii związanych z destylacją przemysłową, co znacząco wpływa na efektywność i jakość procesów produkcyjnych. Innowacje te obejmują zarówno nowe materiały konstrukcyjne, jak i zaawansowane systemy automatyzacji. Wykorzystanie materiałów kompozytowych oraz stali nierdzewnej o wysokiej odporności na korozję pozwala na zwiększenie trwałości i niezawodności urządzeń. Z kolei nowoczesne systemy monitoringu i kontroli procesów umożliwiają bieżące śledzenie parametrów pracy destylatorów oraz szybką reakcję na ewentualne odchylenia od normy. Rozwój technologii cyfrowych, takich jak sztuczna inteligencja czy analiza danych, pozwala na optymalizację procesów produkcyjnych poprzez przewidywanie awarii oraz dostosowywanie parametrów pracy do zmieniających się warunków. Dodatkowo, innowacyjne rozwiązania związane z odzyskiem energii oraz minimalizacją odpadów przyczyniają się do zwiększenia efektywności energetycznej całych instalacji.
Jakie są przyszłe trendy w rozwoju destylatorów przemysłowych
Przyszłość destylatorów przemysłowych zapowiada się niezwykle obiecująco dzięki postępowi technologicznemu oraz rosnącemu naciskowi na zrównoważony rozwój. Jednym z kluczowych trendów jest coraz większe zainteresowanie ekologicznymi rozwiązaniami, które mają na celu minimalizację zużycia energii oraz redukcję emisji gazów cieplarnianych. Wprowadzenie technologii odzysku ciepła oraz zastosowanie odnawialnych źródeł energii stają się standardem w nowoczesnych instalacjach przemysłowych. Kolejnym istotnym trendem jest automatyzacja procesów produkcyjnych – systemy oparte na sztucznej inteligencji będą coraz częściej wykorzystywane do monitorowania i optymalizacji pracy destylatorów, co pozwoli na osiągnięcie lepszej efektywności i jakości produktów. Również rozwój technologii cyfrowych umożliwi lepsze zarządzanie danymi oraz analizę wyników produkcji w czasie rzeczywistym. Warto również zauważyć rosnącą rolę destylacji w przemyśle biotechnologicznym oraz farmaceutycznym, gdzie precyzyjna separacja składników staje się kluczowa dla uzyskania wysokiej jakości produktów końcowych.
Jakie są koszty inwestycji w nowoczesne destylatory przemysłowe
Koszty inwestycji w nowoczesne destylatory przemysłowe mogą być znaczne, jednak warto je rozpatrywać w kontekście długoterminowych korzyści ekonomicznych i ekologicznych. Cena zakupu urządzenia zależy od wielu czynników, takich jak jego typ, rozmiar oraz zastosowane technologie. Destylatory kolumnowe o dużej wydajności będą zazwyczaj droższe niż prostsze modele prostokątne przeznaczone dla mniejszych zakładów produkcyjnych. Dodatkowo koszty instalacji oraz uruchomienia urządzenia również powinny być uwzględnione w budżecie inwestycyjnym. Warto jednak pamiętać, że nowoczesne destylatory charakteryzują się wyższą efektywnością energetyczną oraz mniejszymi stratami surowców, co przekłada się na niższe koszty operacyjne w dłuższej perspektywie czasowej. Dodatkowo wiele firm decyduje się na inwestycje w technologie odzysku ciepła czy systemy automatyzacji, które również mogą przyczynić się do obniżenia kosztów eksploatacyjnych.
Jakie są kluczowe czynniki wpływające na efektywność destylatorów przemysłowych
Efektywność destylatorów przemysłowych jest uzależniona od wielu czynników, które mogą znacząco wpłynąć na jakość i wydajność procesu destylacji. Przede wszystkim, kluczową rolę odgrywa jakość surowców wykorzystywanych w procesie – ich czystość oraz skład chemiczny mają bezpośredni wpływ na końcowy produkt. Kolejnym istotnym czynnikiem jest odpowiednie ustawienie parametrów pracy, takich jak temperatura, ciśnienie oraz przepływ cieczy, co pozwala na optymalizację procesu separacji składników. Dodatkowo, konstrukcja samego destylatora, w tym rodzaj zastosowanej kolumny oraz elementów wspomagających, ma duże znaczenie dla efektywności działania urządzenia. Regularne konserwacje oraz przeglądy techniczne są niezbędne do utrzymania wysokiej sprawności destylatorów. Wreszcie, odpowiednie szkolenie personelu obsługującego urządzenia również przyczynia się do zwiększenia efektywności operacyjnej.